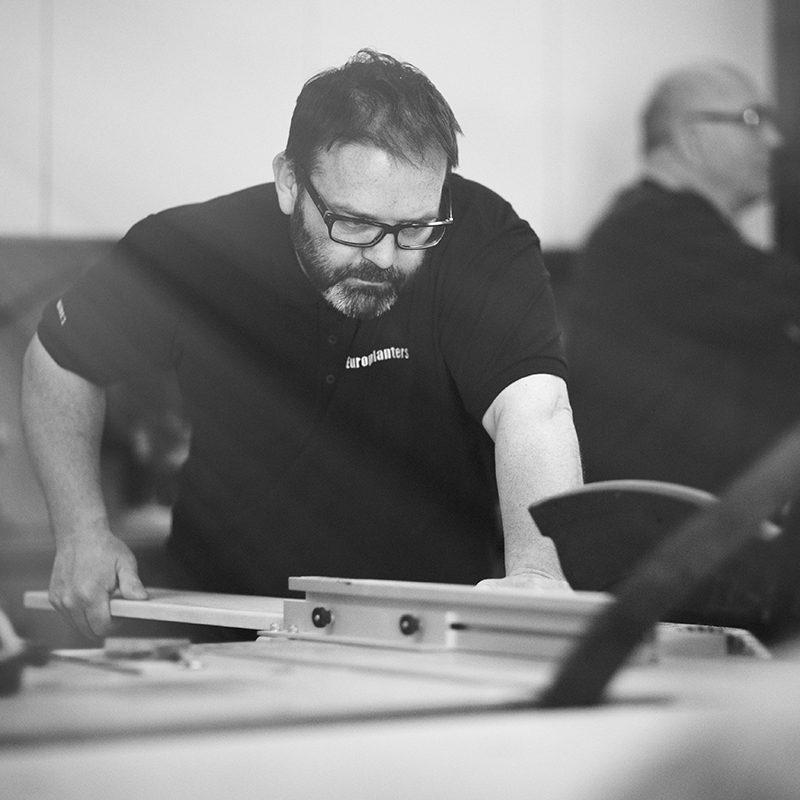
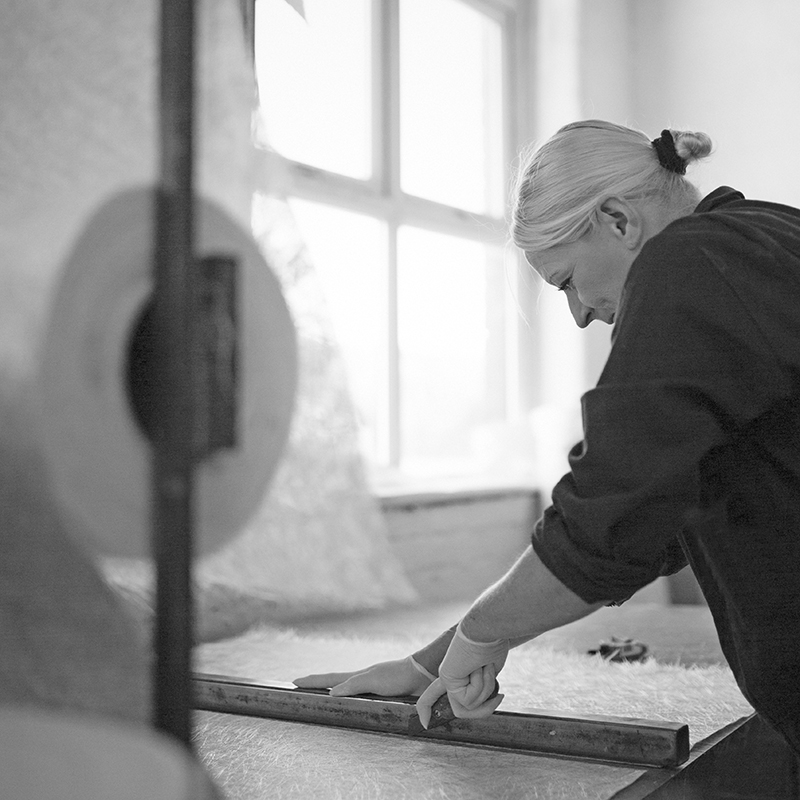
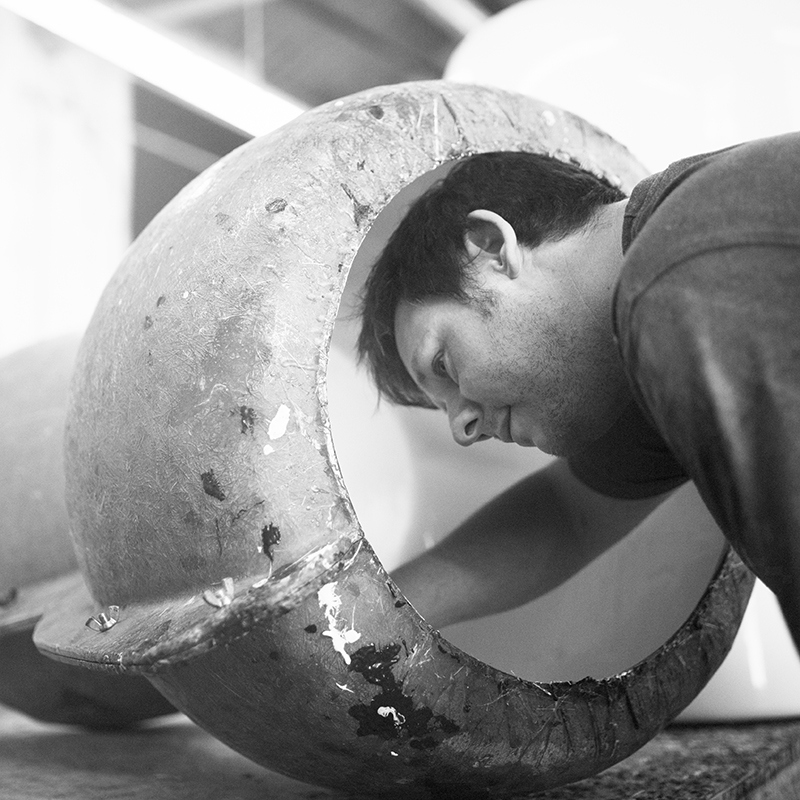
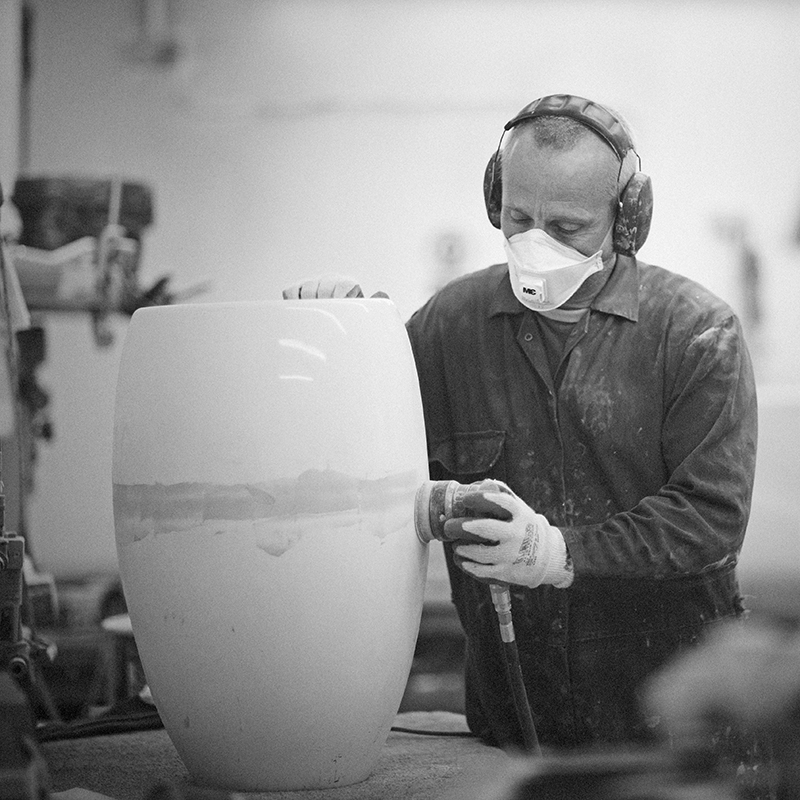
Moulds are created by working with designers from an initial concept right the way through to a finished product. When designing a new product there are several things to consider such as the shape and rim detail. All GRP Planters have to start with a mould and in general they are a two-part mould to accommodate the shape and return lip. Some of our more intricate models require a three-part tool.
Once the design has been finalised, a prototype is made using metal, foam, or timber, this ‘master’ is then sprayed and prepared to make the mould.
This mould is formed from GRP around the prototype which once fully cured needs to be removed from the master, polished and coated in a release system to create a high gloss non-stick surface that will be reflected in the final product.
If a matt or satin finish is required the product is then sprayed with a tough polyurethane or acrylic paint.
Once our mould is ready to use, the product can begin to be made. Gel coat is applied often using a pigment or shade which is closest to the final colour if the product is being sprayed as a final finish. This ensures that the colour of the product runs all the way through.
Layers of resin soaked fibre glass matting are then added to the mould and this is repeated several times depending on the size of the final product. More layers give additional thickness and strength, with the basic principle being the larger the product the more layers are required.
All air must then be removed between layers to avoid weak spots or blemishes. Once air has been removed the fibre glass and resin are left inside the mould to cure. Depending on the size and conditions this may take several hours.
Once cured the product is released from the mould and trimmed to give a neat edge all round.
If the product is going to remain as a gel coat finish, it is then buffed to a high gloss finish. If it needs to be sprayed, the surface is abraded to ensure the paint adheres.
All products are sprayed in an enclosed booth then baked for an hour at 45˚ C.
The mould is then carefully archived in our mould storage facility to be used in your future creations.
share us on…